ShAPE-ing the Future: A New Technique for High-Performance Copper Composites
Copper, the workhorse of the electrical world, has faithfully served us for centuries. From powering our cities to driving our motors, its high conductivity keeps the electrons flowing. But as our appetite for electricity grows, and the need for efficiency becomes ever more pressing, we’re reaching the limits of even the best copper alloys.
That’s where the quest for the next generation of conductive materials begins. We need substances that push the boundaries of electrical performance, offering either higher conductivity or a lower temperature coefficient of resistance (TCR). Why does both matter? Imagine a power cable. A material with higher conductivity at room temperature can carry the same current with a thinner cable, saving weight and materials. Or, a material with lower TCR can handle higher currents without overheating, allowing for more efficient power transmission.
The key lies in unlocking the potential of conductive additives like carbon nanotubes and graphene. These wonder materials boast electron mobility orders of magnitude higher than copper, creating lightning-fast pathways for electron flow. Think of them as superhighways for electrons, compared to copper’s country lanes. However, incorporating these additives into practical materials presents challenges. Dispersion, interface optimization, and cost-effective manufacturing are all hurdles to overcome. Yet, research is making leaps and bounds. Engineers are experimenting with novel architectures, tailoring interfaces for seamless electron transfer, and exploring scalable production methods.
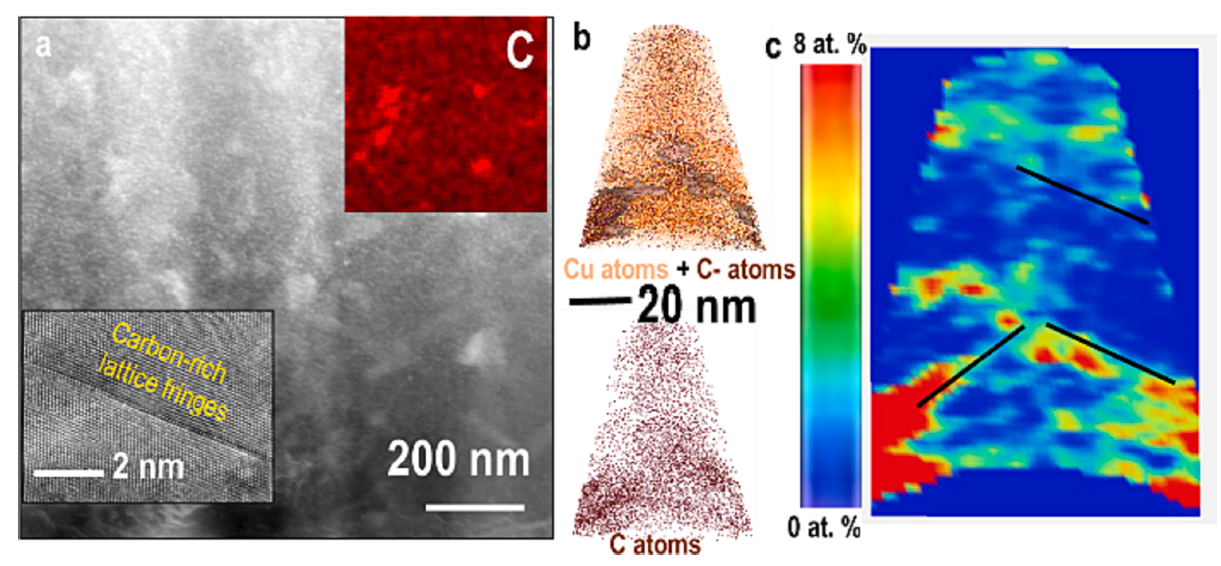
TEM and APT results from Cu-Gr extrudate
Here’s where the research comes in! This groundbreaking work performed by Keerti Kappagantula and team at PNNL has significant implications for the future of energy transport and conversion. The team developed an innovative technique called shear assisted processing and extrusion (ShAPE) to create macro-scale copper-graphene composites with both lower TCR and improved electrical conductivity compared to pure copper.
Using ShAPE, they were able to add a mere 18 parts per million (ppm) of graphene to the C11000 copper alloy and achieve an 11% reduction in its TCR! This is a significant breakthrough, demonstrating the potential of ShAPE for producing high-performance conductors. But how did they achieve this? To understand, they delved deep into the microscopic world using a suite of characterization tools. By analyzing the feedstock and processed samples with advanced techniques like scanning and transmission electron microscopy, they discovered something fascinating.
The ShAPE process transformed some of the added graphene into highly-defected agglomerates while preserving the structure of others, leaving them as smooth mono-to-tri-layer flakes with minimal defects.
They believe this combination of different graphene structures is the key to the observed improvement. The highly-defected agglomerates may act as scattering centers, reducing TCR, while the low-defect flakes enhance electrical conductivity by providing additional pathways for electron flow.
This discovery provides a valuable foothold in the quest for next-generation conductors. The process with its ability to create copper-graphene composites with tailored graphene morphologies, opens exciting possibilities for developing materials with unprecedented electrical performance.
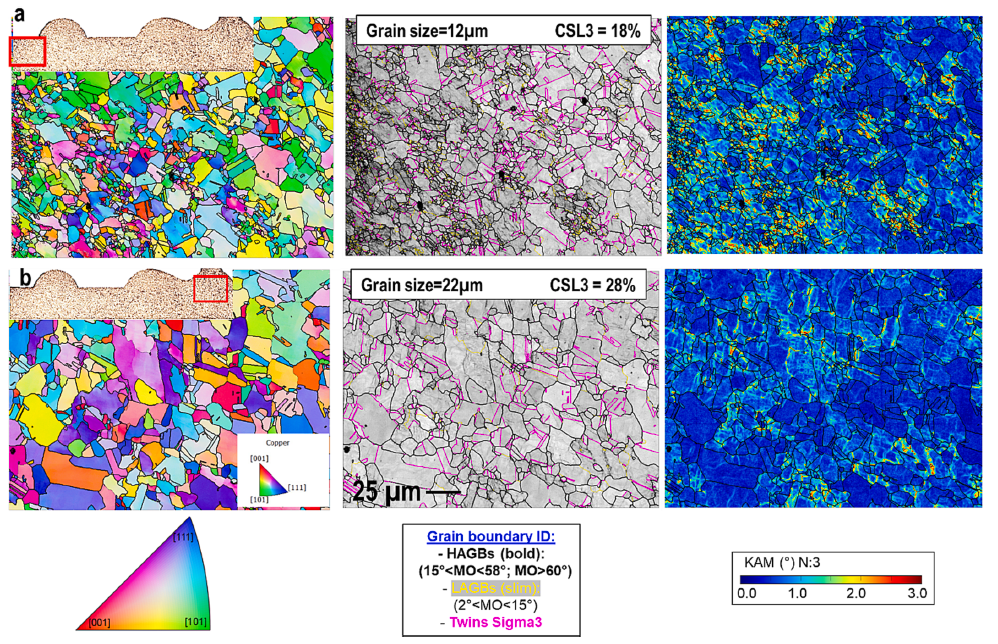
Characterization of Cu-Gr Semi-Extrudate Region
Imagine a future where power cables made from these composites carry energy across vast distances with minimal loss. Or electric motors running with unmatched efficiency, thanks to their low-resistance conductors. These are no longer just dreams; they’re the tangible results of cutting-edge research at PNNL. To read and understand more about the work. Please click the link below
Unprecedented electrical performance of friction-extruded copper-graphene composites
Leave a Reply