
Avoid risks of thermal failures, work with the leader in thermal
Technologies
Expert Thermal is a thermal analysis and design firm. We work with the world’s top tech companies to guide the mechanical hardware design of electronics products of all types, through all phases – from concept, to development, to manufacturing.
Your Trusted Thermal Design Experts
At Expert Thermal, we provide our clients with the assistance and guidance needed to resolve all thermal design issues as early in the product development process as possible to take their product to market as planned with no risk of failure by drawing from the experience working with top Silicon Valley companies like HP, Apple, Cisco, and Tesla. From concept to production, working closely with your in-house engineering teams, we help you through the entire product development cycle; conceptual design, thermal feasibility analysis, baseline CFD modeling, thermal design optimization using CFD simulations, prototype testing, Design-For-Manufacturing (DFM), product thermal and acoustic noise testing and verification. We design the optimal thermal solution for your product, meeting your most competitive product requirements, including the highest functional performance in the worst-case environment, minimum weight, lowest acoustic noise, and smallest form factor at the lowest costs possible.
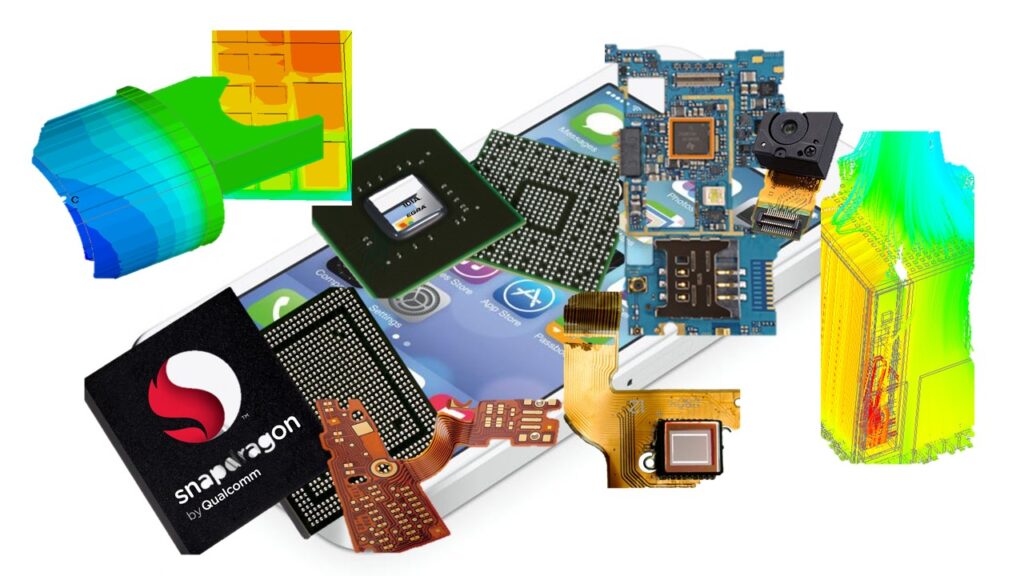
When thermal management isn’t considered in the product design process from the beginning, the product often does not meet the reliability certification requirements resulting in delays in the product release. The losses associated with such delays in releasing the products as planned could be devastating to the company, especially for a startup with the first product to go-to-market .
Having to fix the thermal issues after the product is designed is not only costly but often results in a product that malfunctions and even fail due to thermal stress at unacceptable rates. When the product design lacks consideration for thermal management, the products often don’t meet the marketing requirements for performance and reliability.
Fixing the thermal issues after product design repairs is costly and often does not result in a thermally reliable product. Because of variations in component specifications, the thermal design must not only meet the basic specification but also allow for sufficient margins so that the rate of failure due to thermal is near zero.
When electronics products have little to no thermal margins, their functional performance degrades with time, and their failure rates increase due to exceeding their allowable limits.
Prevent Product Development Obstacles With Thermal Design
Staring thermal design at the conceptual stage not only prevents product release delays and ensures product reliability but also enables the product development team to accommodate changes dictated by new product marketing requirements like the unanticipated higher performance components releases. Chip companies often don’t reveal their roadmap in time, especially to new customers, and may release new chips with higher performance. If the thermal design occurs early in the process, the impact of last-minute changes can be easily assessed and accommodated with no risk. Our thermal engineers will create the required thermal models and conduct the required thermal prototype testing early in the product development process to allow for any potential changes to the product requirements and/or product changes. These validated thermal models we create for your product enable the rapid evaluation of the thermal performance of the product with new changes and modifications of the thermal management solution, including the airflow management system (fans, fan speed, vents, baffles, etc.), heatsinks and thermal interface material (TIM).
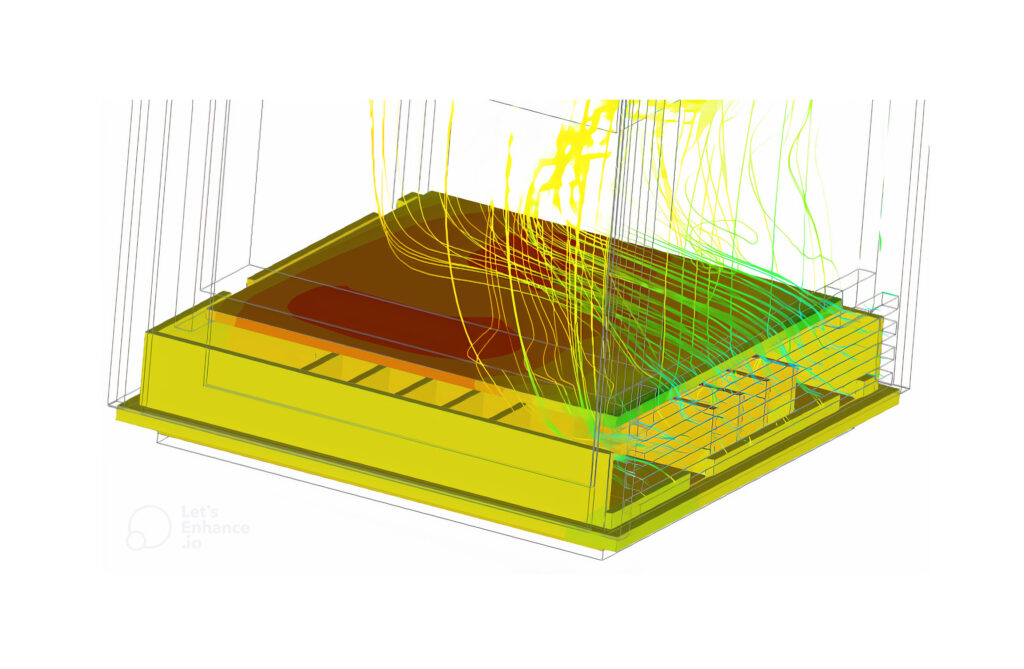
Design for Six Sigma (DFSS) for Thermal Modules:
- Define the Voice of the Customer (VOC): Gather customer inputs regarding thermal performance, noise levels, weight requirements, reliability expectations, and cost constraints. Translate these requirements into measurable metrics for each aspect.
- Identify Critical-to-Performance Characteristics: Determine the critical thermal performance parameters, such as temperature rise, heat dissipation efficiency, noise levels, weight targets, reliability metrics, and cost factors. These parameters significantly impact customer satisfaction and product success.
- Establish Design Objectives: Set specific design objectives for each critical characteristic, considering thermal performance, noise levels, weight optimization, reliability improvement, and cost reduction. Define target values or acceptable ranges for each parameter based on customer expectations and industry standards.
- Design Optimization and Simulation: Utilize advanced thermal modeling and simulation tools to optimize the thermal module design. Perform simulations to assess and refine thermal performance, noise levels, weight distribution, and reliability aspects. Analyze the trade-offs between different design options to find the optimal balance.
- Robust Design and Parameter Optimization: Employ robust design techniques, such as Design of Experiments (DOE) and parameter optimization, to identify and control the key factors influencing thermal performance, noise, weight, reliability, and cost. Determine the optimal design settings that minimize variations and meet the defined objectives.
- Design Verification and Validation: Build prototypes and conduct testing to validate the thermal performance, noise levels, weight targets, reliability, and cost estimates. Ensure the thermal module meets or exceeds the design objectives and fulfills customer requirements. Iterate the design as needed based on validation results.
- Design for Manufacturability (DFM) Considerations: Integrate DFM principles to ensure the thermal module design is manufacturable, cost-effective, and meets the desired performance, noise, weight, reliability, and cost goals. Consider material selection, component placement, manufacturing processes, and assembly techniques that optimize these aspects while maintaining thermal efficiency.
- Statistical Process Control (SPC): Implement SPC techniques during the manufacturing process to monitor and control thermal performance, noise levels, weight variations, reliability factors, and cost aspects. Maintain consistent quality and identify any deviations or trends that require corrective actions.
- Continuous Improvement: Embrace a culture of continuous improvement by collecting feedback from manufacturing, field performance, customer satisfaction surveys, and cost analyses. Use this feedback to drive further design refinements, optimize thermal performance, reduce noise levels, minimize weight, enhance reliability, and achieve cost efficiencies.
By incorporating these DFSS principles, manufacturers can develop thermal modules that excel in thermal performance, noise reduction, weight optimization, reliability enhancement, and cost-effectiveness. This approach ensures the products meet or exceed customer expectations and stand out in the market.
Developing a Thermal Performance Matrix:
Define Performance Metrics: Begin by clearly defining the thermal performance metrics that are relevant to the product or system under consideration. These metrics could include temperature rise, thermal conductivity, heat dissipation efficiency, or any other relevant factors.
- Identify Testing Requirements: Determine the specific tests and measurements required to evaluate the thermal performance. This may involve using specialized equipment, such as thermal chambers, infrared cameras, or thermocouples. Consider the testing conditions, duration, and any specific environmental factors that may impact thermal performance.
- Design Test Setup: Develop a standardized test setup that ensures consistent and repeatable measurements. This may involve creating test fixtures, incorporating appropriate sensors, and establishing calibration procedures for the measurement equipment. Consider factors such as material properties, interfaces, airflow, and any other variables that may affect the thermal behavior.
- Conduct Verification Testing: Perform initial verification testing to validate the effectiveness of the test setup and measurement techniques. This step helps identify any potential issues or variations that need to be addressed before moving forward with mass production.
Developing a thermal performance matrix and measurement method for mass production involves establishing a systematic approach to assess and quantify the thermal characteristics of a product or system consistently. Here is an outline of the process:
Design for Manufacturing (DFM) of Thermal Modules:
Design for Manufacturing (DFM) is an approach that focuses on designing products in a way that facilitates their efficient and cost-effective manufacturing. When applied to thermal modules processes, DFM aims to optimize the design to enhance thermal performance, manufacturability, and quality. Here are key aspects of DFM for thermal module:
- Thermal Management Considerations: DFM for thermal module involves carefully considering the thermal management requirements of the product during the design phase. This includes determining the heat generation and dissipation requirements, identifying critical components or areas prone to overheating, and ensuring adequate heat transfer paths.
- Component Placement and Layout: Optimizing the placement and layout of components is essential for efficient thermal management. Designers need to consider factors such as airflow, proximity to heat sources or sinks, and the use of heat-spreading materials or heat pipes to distribute and dissipate heat effectively.
- Material Selection: Choosing appropriate materials with good thermal conductivity and thermal resistance properties is crucial for efficient thermal management. Designers need to consider the use of thermally conductive materials, heat sinks, or thermal interface materials (TIMs) to enhance heat dissipation and minimize thermal resistance.
- Enclosure and Ventilation Design: The design of the product’s enclosure plays a vital role in thermal performance. DFM for thermal module involves optimizing enclosure design to facilitate adequate ventilation, heat dissipation, and the prevention of thermal hotspots. This may involve incorporating ventilation channels, fans, or heat sinks into the design.
- Design for Airflow: Proper airflow management is crucial for effective thermal management. DFM considerations may involve designing airflow paths, optimizing the placement and design of vents or openings, and minimizing obstructions to airflow within the product.
- Heat Dissipation Mechanisms: DFM for thermal module involves incorporating heat dissipation mechanisms into the design. This may include designing appropriate heat sinks, heat pipes, or other cooling solutions to efficiently transfer and dissipate heat generated by components.
- Design Validation and Simulation: To ensure the effectiveness of the thermal design, DFM may involve utilizing thermal simulation tools, such as Ansys Ice Pak or Fluent, to perform virtual simulations and analyses. This allows designers to evaluate thermal performance, identify potential issues, and make necessary design refinements before manufacturing.
- Collaboration and Iterative Design: Successful DFM for thermal module requires collaboration between design, thermal engineering, and manufacturing teams. It often involves an iterative design process where feedback from manufacturing experts and thermal analysis is incorporated into design revisions to optimize thermal performance and manufacturability.
By considering these DFM principles during the design phase of thermal module, manufacturers can enhance thermal performance, improve manufacturability, reduce costs, and ensure reliable and efficient thermal management in the final product.
DOE and Parameter Optimization
We conduct Design of Experiments (DOE) and parameter optimization to identify and control the key factors influencing thermal performance, noise, weight, reliability, and cost. Here’s an explanation of how DOE and parameter optimization can be applied in this context:
- Design of Experiments (DOE)
DOE: DOE is a systematic approach that involves designing and conducting a series of experiments to gather data and analyze the effects of different factors or variables on the response or outcome of interest. In thermal module, factors can include design variables related to heat dissipation mechanisms, material choices, component placement, insulation, airflow management, and more.
- Identifying Key Factors:
– Define Key Factors: Identify the factors that significantly influence thermal performance, noise, weight, reliability, and cost in the thermal module design. These factors can be determined based on engineering knowledge, literature review, or preliminary studies.
– Determine Factor Levels: Determine the range and number of levels for each key factor. For example, the material factor can have different options like aluminum, copper, or composite, while the airflow rate factor can have low, medium, and high levels.
- Experimental Design:
– Sampling: Generate a set of unique and representative combinations of factor levels. Ensure that the design space is evenly sampled, allowing for a more thorough exploration of the factors and their interactions.
– Conduct Experiments: With the generated experimental design, perform experiments or simulations to collect data on thermal performance, noise levels, weight, reliability, and cost for each unique combination of factor levels. Measure or calculate the responses based on the defined metrics and objectives.
- Response Analysis and Modeling:
– Analyze Data: Analyze the collected response data to understand the relationships between the factors and the responses. Statistical analysis techniques, such as regression analysis or analysis of variance (ANOVA), can help determine the significance of each factor and their interactions.
– Develop Models: Develop mathematical models or response surfaces to represent the relationships between the factors and the responses. These models provide insights into the influence of each factor on thermal performance, noise, weight, reliability, and cost.
- Parameter Optimization:
– Define Objectives and Constraints: Define the optimization objectives, such as maximizing thermal performance, minimizing noise levels, optimizing weight, enhancing reliability, and minimizing cost. Consider constraints such as maximum weight limit, reliability requirements, and cost limitations.
- Sensitivity Analysis:
– Sensitivity analysis can be performed to assess the impact of uncertainty or variations in the factors on thermal performance, noise, weight, reliability, and cost. It helps in understanding the robustness of the optimized design and identifying critical factors that require closer control or consideration.
By combining DOE with parameter optimization techniques, we systematically analyze and optimize the design factors affecting thermal performance, noise, weight, reliability, and cost. This approach allows for a more representative sampling, identifies the key factors, and facilitates the discovery of optimal factor settings. Ultimately, it enables the creation of highly efficient,
Design for Assembly (DFA):
We employ Design for Assembly (DFA) approach that focuses on optimizing the design of a product or assembly to simplify the manufacturing and assembly processes. In the context of a thermal module, DFA principles can be applied to enhance the efficiency, reliability, and ease of assembly of the thermal components. Here’s an overview of Design for Assembly for a thermal module:
- Component Selection and Integration:
– Simplified Components: Select components that are designed for ease of assembly. Look for components that are modular, standardized, and readily available, reducing the need for complex assembly steps.
– Integration Opportunities: Explore opportunities for integrating multiple functions into a single component. This can help reduce the number of components, assembly steps, and potential points of failure.
- Design for Accessibility:
– Accessibility of Components: Ensure that the key components involved in the thermal module, such as heat sinks, fans, or insulation, are easily accessible for assembly and maintenance. Design openings or access points that allow straightforward installation or removal of these components.
– Clearances and Tolerances: Define appropriate clearances and tolerances to facilitate component alignment and fit during assembly. This helps avoid unnecessary adjustments or rework.
- Fastening and Attachment Methods:
– Simplified Fastening: Utilize standard or easily accessible fastening methods, such as screws, snap fits, or quick-release mechanisms, to simplify assembly and disassembly. Avoid complex or specialized fasteners that may require additional tools or time for assembly.
– Self-Alignment Features: Incorporate self-alignment features in the design to aid in the proper alignment of components during assembly. These features can reduce the risk of misalignment or the need for manual adjustments.
- Modular and Subassembly Approach:
– Modular Design: For complex products, divide the thermal module into modular subassemblies that can be independently assembled and tested. This approach allows for parallel manufacturing and assembly processes, reducing overall production time.
– Standardized Interfaces: Establish standardized interfaces between subassemblies to ensure compatibility, easy alignment, and efficient assembly. This enables the interchangeability of components and facilitates repair or replacement if necessary.
- Design for Serviceability:
– Serviceability Considerations: Anticipate the need for service and maintenance activities on the thermal module. Design features such as removable panels, access points, or diagnostic interfaces to facilitate easy maintenance, inspection, or repair of the thermal components.
– Documentation and Markings: Provide clear and intuitive documentation, markings, or labeling to guide assembly and disassembly processes. This can include assembly instructions, part numbers, or identification labels on components for easy recognition.
- Design Verification and Testing:
– Design Verification: Conduct design verification activities, such as virtual simulations or prototype testing, to ensure proper fit, alignment, and thermal performance of the thermal module. Identify potential assembly issues or design flaws early in the development process.
– Design Validation: Perform thorough testing and validation of the assembled thermal module to verify its thermal performance, reliability, and functionality. This includes thermal testing, noise measurement, weight assessment, and other relevant tests.
By incorporating Design for Assembly principles into the design process of a thermal module, manufacturers can optimize the assembly process, improve efficiency, and reduce the risk of errors or complications during manufacturing. Simplifying component selection, enhancing accessibility, employing standardized fastening methods, utilizing modular approaches, and considering serviceability contribute to a streamlined assembly process and ultimately result in a more reliable and cost-effective thermal module.
Manufacturing Process Characterization:
Process characterization is a systematic approach used to understand, improve, and optimize the manufacturing processes involved in the production of a thermal module to enhance its thermal performance. By analyzing and characterizing the manufacturing processes, manufacturers can identify areas for improvement, optimize process parameters, and achieve higher levels of thermal performance. Here’s an overview of how process characterization can be applied to improve and optimize the thermal performance of a thermal module during product development phases:
- Process Understanding:
– Identify Process Steps: Identify the key manufacturing process steps involved in the production of the thermal module. This may include processes such as component assembly, soldering, bonding, thermal interface material application, or encapsulation.
– Define Process Parameters: Identify the critical process parameters that have a significant impact on thermal performance. These parameters can include temperature, pressure, curing time, bonding force, material thickness, or any other relevant variables.
- Measurement and Data Collection:
– Define Performance Metrics: Determine the performance metrics or characteristics that reflect the thermal performance of the thermal module, such as thermal resistance, temperature distribution, heat dissipation efficiency, or thermal stability.
– Establish Measurement Methods: Define the appropriate measurement methods and tools to collect data on the identified performance metrics. This may involve thermal imaging, thermocouples, heat flux sensors, or other measurement techniques.
– Conduct Experiments: Perform controlled experiments to collect data on the performance metrics while systematically varying the process parameters. This allows for the characterization of the process performance and its influence on thermal performance.
- Data Analysis and Optimization:
– Statistical Analysis: Analyze the collected data using statistical techniques to identify the relationships between the process parameters and the thermal performance metrics. This can involve methods such as analysis of variance (ANOVA), regression analysis, or design of experiments (DOE).
– Identify Key Process Parameters: Determine the key process parameters that significantly affect thermal performance. These parameters may have a direct impact on heat transfer, component alignment, material properties, or other factors influencing thermal performance.
– Optimize Process Parameters: Utilize statistical optimization techniques, such as response surface methodology (RSM) or design optimization algorithms, to find the optimal values or ranges for the identified key process parameters. The goal is to achieve the desired thermal performance objectives.
- Process Improvement and Control:
– Implement Process Changes: Implement the optimized process parameters and any recommended process changes based on the findings from the characterization and optimization efforts. This may involve adjustments to equipment settings, material selection, process sequences, or operator training.
– Process Monitoring: Establish monitoring and control mechanisms to ensure the implemented process changes are consistently applied during production. This can involve process control charts, statistical process control (SPC), or real-time monitoring systems to track process performance and detect any deviations.
- Validation and Verification:
– Thermal Testing and Validation: Conduct thorough thermal testing and validation to verify the effectiveness of the process improvements in achieving the desired thermal performance. This may include thermal analysis, thermal cycling tests, accelerated aging tests, or other relevant validation methods.
– Continuous Improvement: Foster a culture of continuous improvement by regularly reviewing and analyzing process performance data, soliciting feedback from stakeholders, and implementing further optimizations or refinements as necessary.
Process characterization allows manufacturers to gain insights into the manufacturing processes’ impact on thermal performance and identify areas for improvement. By optimizing process parameters, making informed process changes, and implementing effective process control, manufacturers can enhance the thermal performance of TLAs during product development phases and deliver products with improved thermal characteristics.
Our Features
and more...
Creative Websites
Adipiscing elit phasellus blanit ma… read more
Contact Forms
Portfolio Pages
40,000 customers in 100 countries use porto template. Meet our Customers.







Latest Posts
What Client’s Say
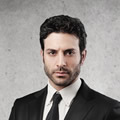
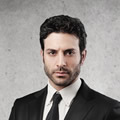